Siemens Digital Industries Software announced today that the latest release of Simcenter™ software for mechanical simulation helps streamline electrification engineering projects, assists new aircraft meet margins of safety, simplifies durability testing across many industries and much more.
“Addressing complex engineering challenges such as developing products that are more powerful, yet greener, lighter yet stronger requires a fully-integrated CAE solution,” said Jean-Claude Ercolanelli, Senior Vice President, Simulation and Test Solutions, Siemens Digital Industries Software. “The latest release of Simcenter offers a host of powerful enhancements to help engineers meet those challenges efficiently and significantly faster than ever before, whether that is getting tire contact simulations solved 45% quicker or reducing airframe structure preprocessing by up to 80%.
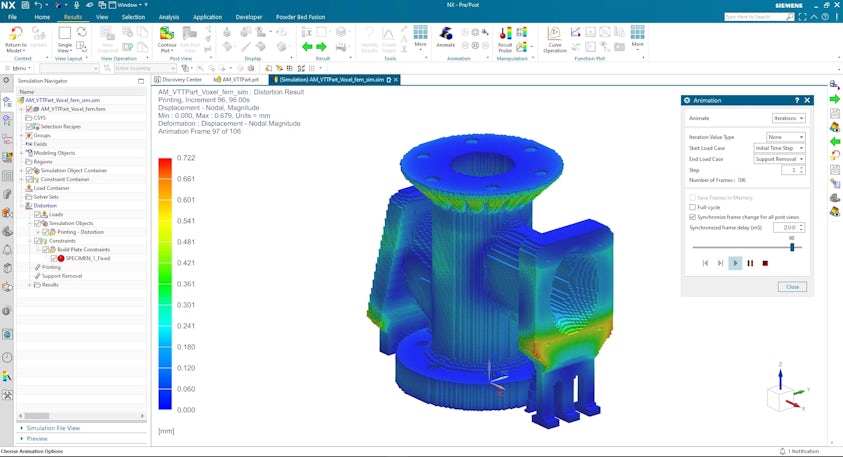
Voxel-based meshing allows non-CAE engineers to produce meshes capable of producing good quality models for most model types – particularly useful for simulating additive manufacturing build methods such as powder-bed fusion (PBF)
The highlights in this release are applicable across all industries and workflows and bring new functionality to the Simcenter family of products. Highlights include:
- For those exploring Additive Manufacturing (AM), build process simulation is a must, particularly when dealing with metals-based powder-bed fusion production methods. The complex nature of these processes usually require the AM engineer to collaborate with an experienced CAE expert. The latest release of Siemens’ Simcenter™ 3D software introduces a simplified application for simulation of the powder-bed fusion (PBF) build process that is easy to use for engineers without in-depth CAE expertise. Using a robust voxel-based mesh in the background, it can quickly model and simulate the PBF build process, allowing engineers to gain a good understanding whether a part will build successfully. More detailed analysis can then be performed by CAE experts also using Simcenter 3D, thus enhancing collaboration.
- Following on from the introduction of the ability to launch simulations on remote HPC systems directly from within Simcenter 3D, engineers now have the ability to review simulation results directly from the Remote Simulation interface. This helps engineers determine if simulation studies ran correctly before transferring large results files back to a local workstation for in-depth evaluation.
Electrification is a major trend across the Automotive industry and development of new Electric Vehicle (EV) powertrains tend to be broken into silos for e-motor design, transmission analysis, NVH and acoustics. Simcenter mechanical simulation tools can help automakers break these silos by helping critical load, design and model information to flow easily between each of these disciplines for EV powertrain development. Beyond EV development, additional new capabilities in this release improve simulation of other automotive applications from NVH, to tires, to windshield wiper performance. Highlights includes:
- The new contact pattern display in Simcenter 3D helps analyze wiper contact patterns. By modeling the wiper as a flexible body combined with contact elements, the new contact pattern display will show easy to interpret results of the wiper forces across the windshield, allowing the user to learn how consistently or inconsistently the forces are distributed and if the wiper design is working as expected, without the need for costly and time-consuming physical testing
- Finally, the latest release of Siemens’ Simcenter™ Tire software has an updated road contact algorithm to reduce the large amount of road data exchange required to build the high-fidelity tire models required for driving simulators and Hardware-in-the-Loop set-ups. This means that computational performance is increased by up to 45% enabling the use of high-fidelity tire models in real-time application.
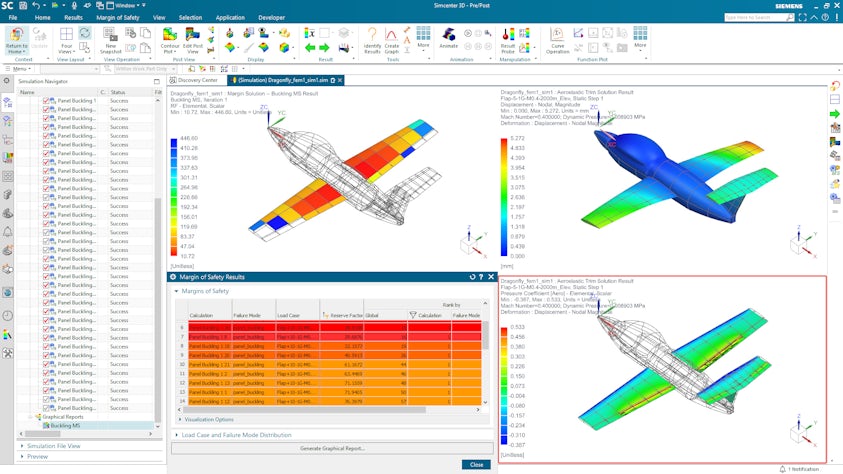
New visual report allows the user to map margin of safety on to the FE model allowing the engineer to generate a contoured view for the margins of safety result table with filters in place.
For the Aerospace industry, new capabilities reduce the number of models needed to simulate the behavior of thin aircraft skins and perform margin of safety calculations more quickly than ever before. In addition to the new improved airframe applications, Simcenter can help engineers better understand rocket launch dynamics by simulating the liquid sloshing in fuel tanks. Highlights include:
- New standard calculation templates have been added to the margin of safety analysis tools within Simcenter 3D. These new templates automatically prefill all the inputs based on a set of rules so the engineer just needs to select the geometry to apply calculation to – removing the traditional reliance of custom script development and the associated maintenance costs.
- A new capability in Simcenter™ Nastran software helps airframe engineers with thin skinned airframe structures that have different stiffness behavior depending on the load case; tension (membrane) vs. compression (shear). Today, engineers typically create multiple models and properties to account for all the different loading conditions. The new tension-only-quad will change from membrane behavior to shear behavior automatically so only a single model is needed to represent an airframe structure - reducing simulation preprocessing time by up to 80%.
- While not isolated to aerospace and rocket applications, liquid fuel sloshing dynamics in storage tanks can pose a challenge to guidance systems. In this latest release of Simcenter Nastran, the new incompressible fluid model helps to predict slosh frequencies and hydro-elastic modes. In other industries, it can also be used for evaluating sloshing in cargo, ballast or fuel tanks of large ships, automotive vehicles, rail cars and much more.
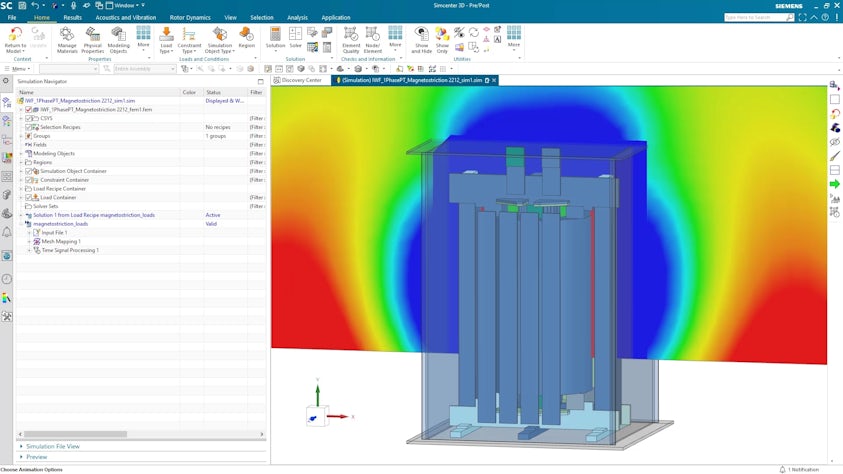
Engineers can now simulate the complex multi-disciplinary magnetostriction effects that cause transformer noise. In addition, you can use these forces directly for noise and vibration assessment without leaving Simcenter 3D
For the Industrial Machinery industry, machine uptime is the prime driver, but machine manufacturers often lack the time or resources to physically test their machines to their limits. Here, Simcenter can help with new capabilities to help durability prediction without the need for specialist knowledge. Highlights include:
- Simcenter 3D overcomes the need for separate toolsets and knowledge for proper durability by streamlining and automating strength analysis. Simcenter 3D can automatically calculate the parameters needed to adhere to the industry standard FKM guidelines. This means engineers can conduct durability analysis directly from their stress analysis results, to ultimately help machines meet operation requirements.
- Industrial power transformers need to meet strict noise emission standards and qualify the EMAG-Acoustics models for transformer development. Simcenter 3D can now simulate the complex multi-disciplinary magnetostriction effects that cause transformer noise very quickly and accurately. Additionally, the forces calculated can be used both for noise and vibration assessment allowing electromagnetics and acoustic performance simulation within a single environment.
- Lastly, industrial machines often have rotating shafts spinning at high speeds which can also vibrate. Engineers use rotor dynamics simulation and Campbell diagrams to understand the vibration frequencies at various operating speeds – but these are only applicable to linear systems. When working with non-linear bushing systems, Simcenter 3D allows the calculation of complex modes during a nonlinear harmonic response to generate a Campbell diagram so that critical speeds of a nonlinear system can be assessed, providing a greater level of understanding of complex rotating components.
Learn more about the latest updates to Simcenter mechanical solutions and discover how the latest simulation enhancements can help streamline workflows and bring greater insight into products performance, by watching this video or by visiting https://blogs.sw.siemens.com/simcenter/simcenter-mechanical-simulation-2212/